
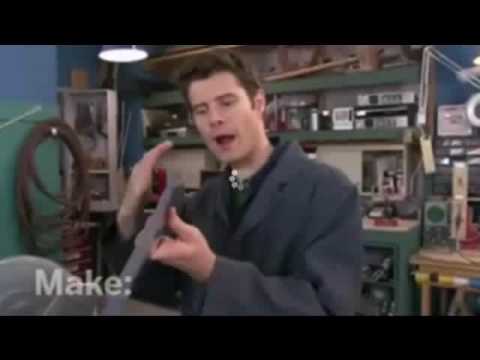
The same can be true for wind-turbine blades.Ĭurrent utility-scale turbines are equipped with blades that range from 40 m (130 ft) to 90-m (300 ft) diameters. With a legacy in aerospace, the software has helped users such as NASA, Lockheed Martin, Boeing, and Bombardier, trim at least 20% of the weight from structures. Lighter weight means better performance, longer life, lower manufacturing costs, and shortened manufacturing cycles, all factors that enhance competitiveness in energy markets. As they grow, blades must be kept as light as possible. To increase the power generating capacity of a turbine, blades must grow in length (power captured by a turbine is proportional to the square of blade length). HyperSizer software performs panel swaps to find one that best meets the design criteria for a particular region of the blade.ĭesign improvements to windpower turbine blades should increase their efficiency and performance, trim the cost of harvesting the wind, and keep it competitive with fossil fuels. Optimizing all possible permutations for a composite laminate design gives engineers control of most every design detail. The software analyzes complex composite structures (it works with metals and other materials as well) by quickly evaluating designs in a ply-by-ply, and even finite element-by-element, manner. The tool couples with FEA in a feedback loop, searching for solutions that minimize weight while at the same time maximizing structural integrity and manufacturability. HyperSizer software, for example, is a composite optimization and structural sizing tool that works out-of-the-box with a wide variety of finite-element analysis (FEA) solvers. With failure rates still high for turbine blades (a Sandia survey of wind energy plants documented rates as high as 20%) and down-time costly and bad for business, blade designers and manufacturers must turn to the best practices for designing composites. Weight is of tremendous importance when designing wind-turbine blades because a lighter blade uses less material, it is easier to manufacture and transport, and has lower fatigue loads ( tweet this). The same is true in the wind-power industry. Those projects must strike a critical balance between low weight and high strength. At NASA Langley Research Center, where I helped develop the code that later became HyperSizer, designs for spacecraft that include composites also have a zero failure-tolerance. The first objective of most any large wind turbine blade design project is to get to the lightest weight possible. HyperSizer can be used to optimize the composite, structure, materials, and layup, resulting in the lightest, most durable design. Engineers at Swiss-based composite manufacturer Gurit peeled back the layers on a generic design to show the complexity of a composite rotor blade.
